金属加工とは
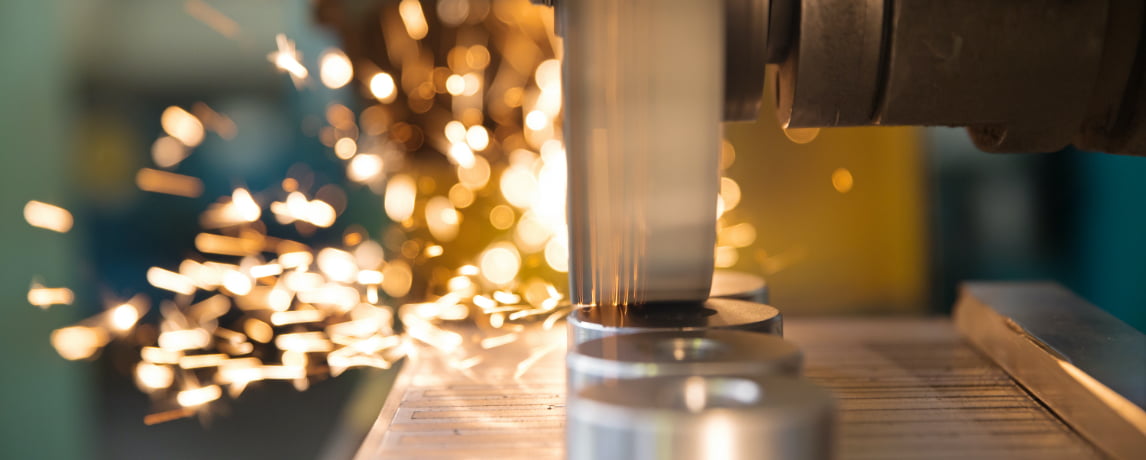
金属加工は切粉が出る加工、出ない加工とがあります。
加工の際に切粉が出る加工を切削加工、出ない加工を非切削加工と言います。
切削加工は切削工具を用いて金属を削りだして製品を制作する加工方法です。
メタルスピードでは金属加工のうち、金属材料を削り出して部品を作成する切削加工から取り扱っています。
目次
メタルスピードが提供する金属加工
徹底したレスポンススピード
今や世界と戦うものづくりの現場では、そのパートナーにもスピードが求められます。メタルスピードは、メインの担当営業の他にサポートの営業も配置することで常に円滑な連絡が取り合えるようにしております。お見積りはご依頼から2時間以内に回答します。
事前のヒアリングを丁寧に行うことが最終回答までの速さ、その後のレスポンスの速さに繋がっております。
加工エキスパートからの目線でご提案
研究開発・設計の試作段階のお客様には、目的を理解した上で加工のプロとしてより良いご提案をさせて頂きます。
部品にはあらゆる面で絶対条件と希望条件があります。
絶対条件が多いほど、コストや納期に影響します。
絶対条件と希望条件を分けてお伺いした上で、最適な加工方法や形状、材料についてご提案をさせて頂きます。
豊富な素材、幅広い加工方法
金属切削加工に使われる材料は多岐に渡ります。
メタルスピードではあらゆる部品の製作に対応する為に機械の充実、加工経験の蓄積を進めています。加工実績はデータにより蓄積され、チームでの情報共有・改善案の適応が行われます。こうして体系化された加工実績が知識・技術として若手も熟練工も使えるものとなり、柔軟な対応を可能にしています。
すべての部品加工をオールインワンで提供することを目指すメタルスピードは、切削加工だけでなく、板金加工や溶接以外にも、表面処理や熱処理、製品の追加工にも対応します。
最小ロット1個から量産に対応
メタルスピードでは1個のみの試作品の他、まとまった数量の生産にも対応します。
スピードが特に重視される一品一様の試作品や治具の製作は主に本社工場で、自社ベトナム工場では量産品をメインに担当し、製造キャパシティを調整しています。
ご依頼内容により、国内協力会社を含めて最適な条件で製作できる場所で製作します。
最短納期のご提案
メタルスピードでは1個のみの試作品の他、まとまった数量の生産にも対応します。
スピードが特に重視される一品一様の試作品や治具の製作は主に本社工場で、自社ベトナム工場では量産品をメインに担当し、製造キャパシティを調整しています。
ご依頼内容により、国内協力会社を含めて最適な条件で製作できる場所で製作します。
検査体制の充実
自社で製作した製品はもちろん、ベトナム工場、協力会社製作分もすべて同じ基準で本社内で検査を行っております。ご要望どおりの製品をお届けするため、営業部・製造部・品質管理部で情報を共有し、各工程でチェックを行っています。
検査機器は各種ゲージの他、三次元測定機、画像測定機、ハンディプローブ測定器など最新のものを導入しています。
取扱素材
納品までの流れ
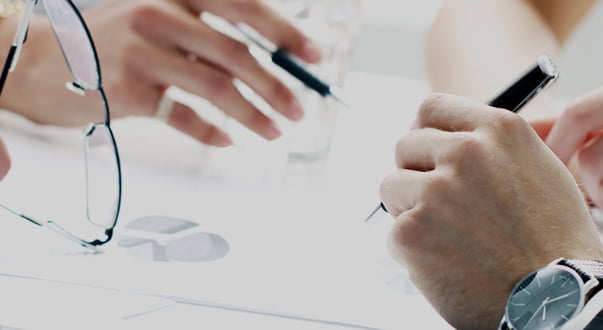
1. お見積りご注文
ご依頼から2時間以内のスピード見積回答製造・研究現場のスピードに対応できるよう、お見積もりは迅速に行います。過去に受注した類似形状のデータから半自動で見積もりを作成するため、業界最速級、平均2時間以内の回答を実現しています。早く製品が欲しい!というお困りの声に、見積もり専任部隊が対応致します。
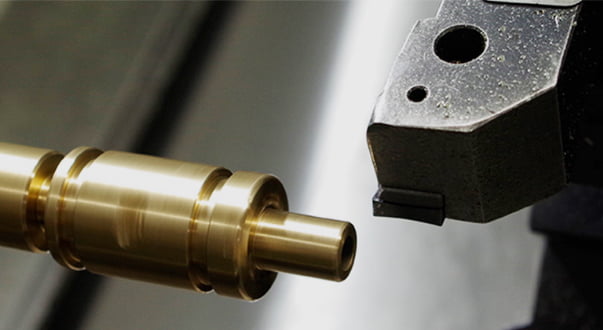
2. 加工
最小ロットは1個から、どんな形状でも対応
新製品のための試作部品や、生産工程改善のための生産部品など「単品1個のみが欲しい」「試作品作りのためのパーツが必要」といったご要望にもお応えできます。これまで培った経験をもとに、複雑または特殊な形状でも対応可能です。経験とノウハウによる的確なご提案をさせていただきます。
2D/3D各種データ・図面なしでも対応可能です。
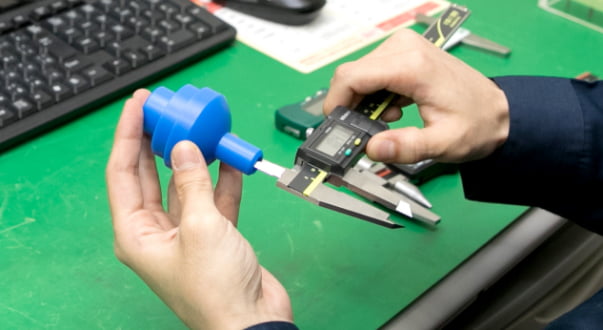
3. 検査
資格保有検査員による徹底した管理体制ミクロン単位の精度を実現するため、25℃に保たれた専用の検査室に、弊社基準の検査資格を有した検査員が常時、三次元測定器や高精度画像測定器など検査器具を用いた寸法検査を行っています。
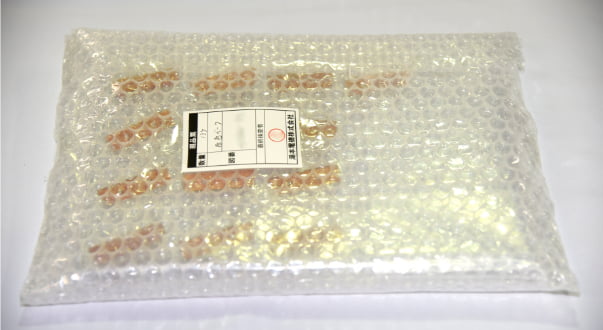
4. 納品・出荷
品質維持のためお届けの梱包にもこだわりを厳しい品質基準の検査を合格した良品をお客様のもとへ確実にお届けするために、担当者が責任をもってひとつひとつ大切に個別包装させていただきます。
金属加工のメリット・デメリット
切削加工で部品を製作する時、部品を使用する環境、要求される性能によっては材料を金属にするかプラスチックにするかで選ぶことができます。
材料によって特性は大きく異なるので、一概に金属とプラスチックを比較する、というのは正確ではありませんが、ここでは金属とプラスチックを比較した際の大まかなメリット・デメリットを挙げていきます。
金属加工のメリット
機械的強度が高い(熱処理が可能)
金属はプラスチックに比べて機械的強度が高い特徴があります。
そのため強度が求められている場所には金属が選択されることが多くなります。
また、必要に応じて熱処理を加えることでさらに強度や靭性を持たせることができます。
耐摩耗性、耐熱温度が高い
プラスチック材料だとスーパーエンジニアリングプラスチックなどを除きほとんどが100℃未満の耐熱温度ですが、金属材料は例えばアルミだと約600℃、鉄で約1200℃、ステンレスで約1400~1500℃と融点が高いので高温下環境での使用に適しています。
なお融点の低いプラスチック材料は、その分自由な成型加工が可能です。
鋼材の体積あたりのコストが低い
一般的なエンジニアリングプラスチックなどと比較すると銅やアルミなどの例外を除き、体積あたりの材料コストは比較的安価です。
切削加工品は、加工性の良し悪しや加工難易度といった加工コストにも注意が必要です。
材料代だけで単純比較するとトータルコストが上がってしまうこともあります。
加工形状が比較的簡単であれば、材料費のウェイトが大きくなるので、材料でのコスト比較が有効になります。
寸法精度が安定しやすい
加工中、刃物と材料の摩擦により熱が発生します。
その熱が影響して対象材料に歪みが生じることがあります。
プラスチック材料は線膨張係数(熱による膨張収縮)が高いため、温度変化による寸法変化が起こりやすいですが、金属材料はプラスチックと比較すると寸法精度は安定しやすい特徴があります。
放電加工やワイヤー加工ができる
金属材料は導電性の材料なので、ワイヤー加工や放電加工での形状再現が可能です。
電気を通すという性質は絶縁性が必要な場合はデメリットにもなる可能性があります。
金属加工のデメリット
切削条件がプラスチック材料より悪くなる
金属と樹脂を比べると、金属の方が硬いので、樹脂ほど工作機械の送りを速くすることはできません。
加工内容や材質によっては刃物回転数の上げられる工作機械や剛性の必要なマシニングを使用する必要があります。
刃物の摩耗もその硬度や材料特有の性質により大きくなるので、プラスチックよりも刃物の消耗を考慮しないといけません。
表面処理を行わないと腐食しやすい
プラスチックだと錆が発生することはありませんが、金属材料は素地の状態だと腐食が進みます。
錆びにくいアルミやステンレスも、酸化被膜は決して完全なものではないので条件次第で腐食が進んでしまいます。
こういった腐食を防ぐために、金属材料には人工的に表面処理(メッキや塗装、封孔処理、表面改質など)を行う必要があります。
薬剤への耐性もプラスチック程ではありません。
家庭用など日常多くみる容器がプラスチックを採用しているのも、これが理由の1つです。
比重がプラスチックに比べて大きい
金属材料はプラスチックに比べると比重が高いものが多いです。
一般的なプラスチックと比べても同じ体積だとアルミでも約2倍、鉄だと約6倍程の重量があります。
重いということは、それだけ部品や装置の重量を増やすことになるので、搬送コストや動力エネルギーが必要になります。
取り扱い中の怪我の可能性が高い
切削加工の現場においては同じ作業をしていても、切り傷などのリスクはプラスチックに比べて重さと硬さのある金属の方が大きくなります。
同じように部品を取り扱うお客様においても同じリスクがあります。
その為、鋭角となる箇所は面取り、バリ処理を行うようにしております。
面取り不要な箇所があれば最低限の角処理にて対応致します。
金属加工の種類
金属加工の方法は大きく分けて4つあります。
専用機械で金属を加工する機械加工、金属を加熱・冷却して性質を変化させる熱処理加工、金属の表面に特性を付与する加工をする表面処理、3Dプリンターによる造形の4つです。
機械加工
金属加工と言うと切削加工やレーザー加工などの他にも、様々な種類があります。
それぞれ専用の機械を用いて加工し、これを機械加工と呼びます。
機械加工は工作機械や加工方法によって【成形加工】【除去加工】【付加加工】【仕上げ加工】の大きく4つに分類されます。
成形加工
成形加工は、原料である金属や非金属を特定の形に成形する加工です。
成形加工には代表的な加工方法が三つあります。
高温の液体金属を鋳型に流し込み固める「鋳造」、二つの型の間に三次元形状の材料を挟み押し固める「樹脂成形」、金属材料の可塑性を利用し圧力を与える、または衝撃を与えて任意の形に成型する「鍛造」があります。
工作物を生成する以外にも金属や樹脂など様々な材料を生み出す際にも用いられる加工方法です。
鋳造
鋳造は、加熱すると溶融し冷却すると凝固するという金属の性質を利用することで金属部品を生成する加工方法です。
型に溶融した金属を流し込み、冷却して型から取り出すことで製品(鋳物)を生成します。
またこのとき使用した型のことを鋳型と呼びます。
鋳造は大量生産時には低コストとなりますが、精度や強度が低い傾向にあります。
製品の精度が必要な場合は、「ろう」を使ったロストワックス法や溶解した金属を高圧で流し込むダイカスト法を用いることもあります。
樹脂成形
樹脂成形では二つの型、雄型と雌型の間に三次元形状の材料を挟み込み、加圧して製品を生成します。また樹脂の靭性や弾性を活かし、型の表面に加圧や空気圧で張り付けて成形するブロー成形や真空成形などもあります。
前者は主に樹脂製品の大量生産、後者のブロー成形は主にペットボトルに真空成形は外装、トレーなどに用いられます。
鍛造
鍛造は材料の可塑性を利用した成形方法となります。
可塑性とは外部からの力を与えて形状を変化させた後、外部から力を与えるのを止めても形状を維持できるという性質です。
金属、樹脂ともにこの性質を持つ材料があり、常温で変形しにくい材料でも熱を加えることで塑性加工が可能となるものもあります。
鍛造は型や工具、治具などを用いて衝撃を与えたり圧力を加えたりをすることで形状を変化させる成形方法で、主に常温で成形する「冷間鍛造」と加熱して成形する「熱間鍛造」とに分かれます。
付加加工
付加加工とは板金加工や結合加工のことを示します。
板金加工は刃物や特殊な工具を用いて材料を切断することで、高強度の金型で薄い金属板を加圧して成形するプレスが一般的に認知されています。
結合加工については金属と樹脂で方法が異なり、金属の場合は熱により金属同士の接地面を溶融し結合します。
樹脂の場合は熱による溶融の他にも有機溶媒により溶解し結合する方法、接着剤のような異種素材を結合媒体にすることもあります。
板金加工
板金加工は、常温または加熱状態の薄い鉄板、銅・銅合金板、アルミニウム・アルミニウム合金板、ステンレス板などを上型(パンチ、ポンチ)と下型(ダイ)で切断または打ち抜く加工方法です。
プレスは様々な形状の金型を取り付けることで曲げ、打抜き、型打ち、絞りなどの加工が可能です。
金属板を必要な形に打ち抜く型を「打抜き型」、任意の角度の溝が付いた型を使用し必要な角度に曲げる型を「曲げ型」、板の外径や縁(ふち)を丸める加工を「巻き型」、穴を開けずに底面のある形状に曲げる型を「絞り型」、数ヵ所を一度に曲げることで複雑な形状を成形する型を「総型」と言います。
板金加工に用いられる機械はプレスと呼ばれ機械式と液圧式の二種類に分類されます。
機械式プレスはフライホイールの回転運動を直線運動に変化させ、液圧式プレスは水圧や油圧によるエネルギーを直線運動に変化させることでプレス加工を行います。
一般的なプレスは加工速度、価格の安価な機械式プレスが用いられます。
※板金加工は材料の形状を変化させる際に可塑性を利用していることから、広義で成形加工に分類されることもあります。
溶接
溶接は複数の金属を加熱し結合させますが、結合方法によって三種類に分けられます。
金属の接合部を加熱し溶融させて結合させる「融接」、複数の金属の接合部を溶融、半溶融状態にして外部から力を加えることにより結合させる「圧接」、結合させる金属同士よりも融点が低い金属を媒体として結合させる「ろう接(ろう付け)」があります。
融接はアーク溶接やガス溶接で、結合させたい金属同士の一部を溶かすことで結合させる結合方法です。
アーク溶接とは母材(金属)と溶接棒(電極)と呼ばれる金属片を用いて、溶接棒に電流を流すことで発生するアーク熱により溶着金属を生成し、母材同士を結合させる方法です。
ガス溶接はアセチレンガスと酸素の混合気に点火し約3200℃の熱により溶接棒を溶かし、母材同士を結合させる結合方法です。
圧接は金属に通電した際に生じるジュール熱を用いて母材同士を加熱し、同時に外部からの圧力を加えて接合させる結合方法です。
接合のさせ方によりスポット溶接(点溶接)、プロジェクション溶接(突合せ溶接)、シーム溶接(継目溶接)と名称が異なります。
スポット溶接は二枚の母材を重ねて棒状の固定電極から電流を流し加熱、同時に加圧して溶接します。
プロジェクション溶接はスポット溶接と同じく母材を重ねて、一方の母材に突起を付け通電し突起部が溶けた箇所を加圧して圧接します。
シーム溶接は電極にローラを用いて重ねた母材を縫合するように溶接する方法で、気密性が必要な際に選択されます。
しかしながら、融接や圧接の溶接加工は母材同士を高温に加熱するため変形やひずみが生じやすく、結合面に盛り上がりや溶接痕が残ってしまい精度が必要な製品を作製することが困難です。
そんな場合には、ろう接により結合します。
ろう接は母材よりも融点の低い金属(銀、銅、アルミニウムなど)を溶かし、母材同士を結合する接着剤として使用する結合方法です。
母材よりも融点が低い素材を接着材として使用するため再び加熱することで分離することも可能です。
溶接はものづくりをする上で様々なメリットがあります。
通常、加工品同士を嵌め合わせる際には加工品同士のクリアランスや構造を入念に計画しなければならず、結合にボルトやリベット、ナットが必要になる場合もあります。
このような場合、溶接であれば構造を簡素化することができ、重量や材料の軽減にもつながります。
しかし溶接部の急加熱および急冷による材質特性の変化、変形、残留応力やひずみ、クラックが生じるなどのデメリットもあるので注意が必要です。
鍛造
鍛造は材料の可塑性を利用した成形方法となります。
可塑性とは外部からの力を与えて形状を変化させた後、外部から力を与えるのを止めても形状を維持できるという性質です。
金属、樹脂ともにこの性質を持つ材料があり、常温で変形しにくい材料でも熱を加えることで塑性加工が可能となるものもあります。
鍛造は型や工具、治具などを用いて衝撃を与えたり圧力を加えたりをすることで形状を変化させる成形方法で、主に常温で成形する「冷間鍛造」と加熱して成形する「熱間鍛造」とに分かれます。
除去加工
金属や非金属を加熱、加圧、衝撃を与えて形状を変化させる成形加工とは異なり、現状の形状を様々な刃物や砥石、電気的エネルギー等を用いて除去することで目的の形状に変化させる加工方法の総称です。
運動エネルギーを刃物に伝達させて工作物の不要箇所を除去する加工を切削加工、電気的エネルギーや特殊なエネルギーを用いる加工方法を特殊加工といいます。
切削加工
切削加工は使用する加工機によって加工方法が異なります。加工機の種類は多々ありますが代表的なものを下記にて説明します。
旋盤
旋盤は工作機械の中で最も基本的な切削加工機です。
その仕組みは旋削対象(材料・工作物)に回転運動を与え、刃物を旋削対象に添わせて不要な箇所を削り取っていきます。
一般的な旋盤には主軸、刃物台はもちろんですが「心押台」と言う機構が取り付けられています。
これは工作物が長い場合、芯(外径が仕上がっていない)が出ていない場合に旋削対象を抑えることで旋削対象の振れの防止に役立ちます。
他にもセンタ穴(中心穴)を空ける際にも用いられます。
一般的な旋盤は横型ですが、縦型旋盤も存在します。縦型旋盤は水平で大きなテーブル上面に旋削対象を固定し回転運動を与えることで、横型旋盤には取り付けられないほど大きい工作物や重量物を旋削する際に利用されます。
フライス盤
フライス盤は前述した旋盤とは異なり、工具(刃物)に回転運動を与え、固定した工作物を指定の形に加工する工作機械です。
工具を取り付ける主軸は、上下(Z軸)に可動し工作物を固定するテーブルは左右(X、Y軸)に可動させることが可能です。
主軸がテーブルに対して垂直のフライス盤を「立フライス盤」、水平のフライス盤を「横フライス盤」と呼び、立フライス盤が一般的に使用されます。
立フライス盤は正面フライス工具、エンドミル、ドリルなどの工具を主軸に取り付け、平面加工、側面加工、穴あけ、段加工、溝加工など多彩な加工が可能です。
横フライス盤も可動方法は同じですが、主軸に取り付けられる工具の種類が少なく、主な加工は切断加工や溝加工のみとなります。
NC工作機械
NCとはNumerical Controlの略であり、特定の数値や記号を機械に読み込ませ自動運転させるシステムのことです。
このシステムを導入し、数値データを電気的信号に変換させて操作する工作機械をNC工作機械と言い、NC装置を導入したフライス盤をNCフライス盤、旋盤に導入した工作機械をNC旋盤と言います。
このNC装置に対話型のプログラムが組み込まれた工作機械をCNC工作機械と呼び、一般的にはCNC旋盤が主流です。
またNC工作機械の中でも自動工具交換機能(ATC)を有するNCフライス盤のことをマシニングセンタと言います。
マシニングセンタは通常のフライス盤と異なり、工具を取り付けるホルダーを複数有しています。
そのホルダーから平面加工、側面加工、穴あけ、タップ加工、溝加工など様々な加工に必要な工具を自動で交換し、加工プログラム通りに加工します。
複合旋盤
通常の旋盤加工は、旋削対象を取り付けた主軸を回転させ固定された工具を添わせることで加工しますが、複合旋盤は主軸を固定またはゆっくりと回転させることで、刃物台の刃物を回転させてドリル加工やタップ加工も可能です。
このように刃物台に取り付けた刃物を回転させることが出来る複合旋盤をターニングセンタといいます。
また旋回ミリング主軸頭というマシニングセンタと同様の切削機能を搭載した複合旋盤では、マシニングセンタのようにドリル加工、エンドミル加工をすることも可能です。
また複合旋盤は二つの刃物台と向かい合わせに二つの主軸が搭載されており、自動で工作物の受け渡しが可能です。
そのため一回のチャッキングで工作物の表側、側面の加工はもちろんのこと、裏側の加工も可能です。
5軸同時制御機械
フライス盤、マシニングセンタの加工は主軸の上下(Z軸)、テーブルの左右(X、Y軸)の3軸を可動させることで工作物を加工します。
5軸同時制御機械はこの3軸に回転軸(A、BまたはC軸)を追加した工作機械です。
主軸が旋回する主軸旋回形とテーブルが旋回するチルトテーブル形があります。
5軸加工は加工面が自由曲面である複雑な加工はもちろんのこと、3軸加工の際に工具の突き出しを長く保たなければならない加工、3軸同時加工(倣い加工)で時間を要する加工の時間短縮にも可能となります。
ボール盤
ボール盤は主軸をベルト駆動により回転させ、取り付けたドリルやタップなどの刃物を下降させることで工作物と接触させて穴あけ加工やタップ加工をするための工作機械です。また、取付け工具を交換することでドリル加工、タップ加工、リーマ加工、センタ穴加工、ザグリ加工、皿モミ加工などの加工が可能です。
一般的な立形ボール盤の他にも主軸が前後稼働可能で広い範囲の加工が可能なラジアルボール盤、同時に複数個所の加工が可能な多軸ボール盤などがあります。
ブローチ盤
ブローチ盤と一般的には聞きなれないかもしれませんが、キー溝加工やスロッター加工が可能な工作機械です。
前工程であけた穴の内径部にブローチと呼ばれる工具を接触させ、引き抜くまたは押し出すことでキー溝やスロッター加工の切削が可能となります。
スプライン加工の内歯(雌型)の加工もブローチ盤で加工が可能です。
研削盤
研削盤は「砥石車」という円形の研削砥石を高速回転させ、工作物に接触させることで加工する工作機械です。
一般的には板状の工作物を加工する際は平面研削盤、円筒状の工作物を円筒研削盤・内面研削盤、心なし研削盤などで加工します。
平面研削盤は工作物をフライス盤のように地面と平行なテーブルに固定し、砥石車の円周面を工作物に接触させることで工作物を平面に加工します。
円筒研削盤は旋盤と同様にチャックに工作物を取り付け回転または固定し、砥石車を工作物に添わせることで外径を加工することが出来ます。
内面研削盤は円筒研削盤と異なり、円筒状の工作物の内径を加工します。
主軸に工作物を取り付け、主軸の向かい合わせに設置された砥石軸には小径の砥石車を取り付けます。
高速回転させた砥石車を回転する工作物の内径に接触させることで内径を仕上げていきます。
心なし研削盤はテーブルやチャックで工作物を固定せず、送り用の砥石車と研削用の砥石車の間の隙間に入れます。
その後、指定の形状に仕上がった工作物が受け台に落下します。
心なし研削盤は円筒研削盤に比べると品質は劣ります。
特殊加工
切削加工とは異なり、刃物ではなく電気エネルギーを用いた放電加工やワイヤー加工、光エネルギーを用いたレーザー加工などを特殊加工と呼びます。
放電加工
放電加工は工作物と電極の界面に放電を起こし工作物の不要な箇所を溶解させる加工方法です。
切削加工に比べて一度に除去出来る量が少ないため加工時間を要しますが、スイッチング回路と言う機能により硬度の高い難切削材も加工できる特徴を持ちます。
また使用する電極の形状を変化させることにより、切削加工では刃物規格が無い形状、刃物が入らないような箇所への加工も可能です。
電極材には銀、銅、タングステン、グラファイトなどが母材として使用されています。
ワイヤー加工
ワイヤー加工はワイヤーを電極として用いた放電加工の一種です。
直径Φ0.02~0.2ほどの細いワイヤーを使用するため、電極材を使用するよりも細い加工が可能となります。
ワイヤーを母材の上下に張るため、立体的な形状では不向きになる場合もあります。
レーザー加工
レーザー加工は、大気中で使用可能な点、集光度が良い点から炭酸ガスレーザーが主に用いられます。
光エネルギーを用いるためより小さな直径で加工が可能な為、難切削材の切断や穴あけ、溶接などが可能となります。
表面処理
機械加工後に研磨処理、罫書き、やすり、表面処理を施します。
研磨処理
研磨処理は除去加工の際に説明した砥粒加工とは少し異なり、工作物の外観や指定面の美化に関わる加工となります。
主にバフ研磨、バレル研磨、ベルト研磨などが一般的です。
バフ研摩は布や皮、フェルトを何層に重ねた円筒状の「バフ」に研磨剤を塗布して研磨対象物または研磨箇所に押し当てる加工方法です。
バレル研磨は多角形のバレル容器に研磨材と研磨対象物を入れ、バレル容器を回転させることで研磨対象物のバリやスケールを無くす加工方法です。
ベルト研磨は砥粒を付着させた布ベルトを専用の機器に取り付けて回転させ、研磨対象物に押し当てることで任意の箇所を研磨する加工方法です。
罫書き加工
主にトースカン、けがき針、ポンチなどを用いて工作物に加工の指標となる印を付けることを罫書きと言います。
加工後に罫書きをすることもあり、その場合は加工品を使用する際の目印にすることが多いです。
また加工品の測定器として使用するハイトゲージとトースカンを組み合わせ、精密に平行線をけがく加工方法もあります。
やすり加工
やすりを使用し工作物の面を滑らかに研磨する加工をやすり加工と言います。
やすりには面の凹凸で種類や用途が異なります。
主に単目、複目、鬼目、シャリ目に分類され、金属や樹脂の仕上げ加工には単目と複目が推奨されます。
特に単目は切れ味が良い上に加工後の傷が目立たないため非金属や軟質金属の加工に用いられます。
一方、複目は古くから普及しているため様々な材料の仕上げ加工に用いられています。
表面処理
表面処理には、機械加工後に加工品の表面を硬化させる処理、被膜を形成し耐食性を向上させる被膜処理、化学反応を利用した化成処理があります。
また他にも樹脂表面にゴムや樹脂のコーティングをするライニング処理があります。
A.硬化処理
金属表面を硬化させる主な処理は、「浸炭焼入れ」「窒化処理」があります。
どちらも金属の熱処理の分類にも含まれますが、表面を変化させる処理として表面処理に分類することもあります。
浸炭焼入れは、木炭や天然ガス、都市ガスなどの浸炭剤を用いて加工品表面に炭素を浸透させた後、焼入れ・焼戻しをして表面硬化する表面処理です。
窒化処理は、加工品表面に窒素を浸透させることで鋼と窒素を反応させて窒化物を生成します。
この窒化物は非常に硬いため、浸炭焼入れのように浸炭後の焼入れ処理は必要ありません。また従来はアンモニアガスを用いて長時間・高温条件下で窒化処理をしていましたが、真空条件下で放電処理を施し、短時間で処理が可能となったイオン窒化(プラズマ窒化)と言う窒化処理も普及しています。
B.被膜処理
対象の金属よりも腐食しづらい金属の被膜を生成することで対象金属の耐食性を向上させる処理方法です。
主に電気めっき、溶融めっき、溶射があります。
電気めっきは金属イオンを含むめっき液に対象の金属を入れ、通電させることで対象の金属表面に溶液中の金属イオンを析出させることで被覆させる方法です。
電気めっきは比較的コストが安く、短時間でのめっき処理が可能ですが、複雑な形状の加工品に対して均一にめっきができないといったデメリットもあります。
また似た処理方法で無電解ニッケルメッキがありますが、電気めっきは電気的処理により酸化還元反応を促しますが、無電解ニッケルめっきは還元剤の酸化による電子の移動を利用したメッキ方法です。
そのため無電解ニッケルめっきは電気めっきには含まれません。
無電解めっきは通電を行うことなくめっき液に浸漬するだけですので、金属素材の種類、様々な形状に関係なく均一性のあるめっき皮膜が可能ですがコストが高く、時間がかかるといったのがデメリットです。
溶融めっきは金属が溶融している容器に対象金属を侵漬し一定時間で引き上げることで表面に溶融金属を被覆する方法です。
その処理方法からドブづけと呼ばれることもあります。
溶射とは高温で溶融した金属を処理対象の金属表面に吹き付けることで被覆します。
C.化学処理
化学反応を利用した表面処理で広く普及しているもので「クロメート処理」「アルマイト処理」「パーカー処理」「黒染め」があります。(下表参考)
クロメート処理 |
通常、クロメート処理単体での処理はせず、亜鉛めっき処理を施した金属加工品をクロム酸溶液に入れることでクロメート被膜を形成させる処理をします。 これは金属に亜鉛めっきのみを施した場合、空気に触れることで酸化や変色、指紋が付きやすいなどの欠点を補うためです。 加工現場の図面内には「クロメート処理」と記載されることが多いですが厳密には間違いで正しくは「亜鉛めっきクロメート処理」となります。 |
アルマイト処理 |
アルマイト処理はアルミニウムに施される表面処理です。 アルミニウムを陽極(+極)で電解処理して人工的に酸化皮膜(アルミの酸化物)を生成させる表面処理のことです。陽極酸化処理(アルマイト)を行うことによって、耐食性や耐摩耗性の向上の他に、本来金属であるアルミニウムに、アルマイト皮膜(酸化アルミニウム)覆うことで絶縁性となり、電気を通さなくするといった効果も付与されます。 アルミニウムは錆びにくい素材で有名ですが、白い錆が出ることもありアルマイト処理によって耐食性を向上させます。 近年では外観美化のためにも施されることも多く、様々な色のアルマイト処理が普及しています。 |
パーカー処理 |
リン酸亜鉛皮膜やリン酸鉄皮膜、リン酸マンガン皮膜など化成させたい皮膜に合わせた溶液を用いて、金属の表面にリン酸塩の皮膜を作り覆う方法です。 寸法公差の厳しいもので、耐食性や潤滑性など機能を要求する場合に適しています。主に鉄鋼全般に使用されますが、鋳物に対して処理すると表面が少し赤くなります。 |
黒染め |
高温で濃度の濃いアルカリ溶液を煮沸し、鉄の表面に四酸化三鉄の皮膜を作って覆う処理方法です。 素材自身の反応によって皮膜を形成するため、寸法の増減はありません。 寸法公差の厳しいもので、黒色特性を要求する場合によく使用されます。 こちらも鉄鋼全般に使用されますが、リン酸塩皮膜処理と同様、鋳物に対して処理すると表面が少し赤くなります。 |
熱処理加工
熱処理加工は、素材を加熱、冷却することによって、硬度や組織を変化させる加工です。
ここでは鋼を主とした金属の性能を向上させる熱処理加工の種類を説明します。
熱処理加工では基本的に、形を変えずに性能を向上させることができます。
多くの産業機械に使用される部品は、熱処理により、必要な性質を付与しています。
変化させる性質については、硬さ・強さ・粘り・耐摩耗性・耐衝撃性・耐腐食性などが挙げられ、金属加工の一種に分類されます。
対象の製品全体の性質を改善する全体熱処理と表面の性質のみを改善する表面熱処理に分かれます。
熱処理加工の種類
熱処理には、焼入れ・焼戻し・焼なまし・焼ならしの4つの加工方法があります。
焼入れ
鋼を硬くします。
一般的な鋼は約700°Cで、結晶構造や性質の変化が起こります。
この性質変化を「変態」、その変化がはじまる温度を「変態温度」と呼びます。
焼入れは、鋼を高温に加熱してオーステナイト組織にした後、急冷します。
このオーステナイト組織というのは、変態温度を超え、鋼が軟らかくなる状態のことです。その後に鋼が黒づく温度(約550°C)まで冷却すると、オーステナイトは硬いマルテンサイトという組織に変化します。
ここまでの工程によって、鋼は硬くなりますが、そのままではもろく割れなどが生じやすい状態です。
焼戻し
鋼を強くします。
焼入れをした後には必ずこれを行います。
基本的に、焼入れと焼戻しはセット行うものです。
焼入れだけの鋼は、すぐに割れたり傷が付いてしまいます。
この処理の目的は、硬さの調整・内部応力の除去・靭性(ねばり強さ)の付与です。
焼戻しには、以下の2種類があります。
・低温焼もどし
焼もどし温度は150~200℃で、靭性より硬さを優先するのが一番の目的です。この温度では硬さの減少はわずかなので、工具や刃物、ゲージなどに行います。
・高温焼もどし
焼もどし温度は550~650℃で、硬さは落ちますが、靭性は大きくなります。それが高温焼もどしの一番の目的です。
焼入れと高温焼もどしの工程を併せて、調質と呼びます。硬さと靭性を兼ね備えた、強靭な鋼になるので、歯車やシャフトに行います。
焼なまし
鋼を軟らかくします。
鋼は硬い方が良いのではないか、と思ってしまいますが、加工をするためにはある程度の軟らかさも必要です。
それがこの処理で焼鈍または、アニーリング処理と呼ばれます。
焼なましの目的は、鋼の組織改善、鋼の軟化です。
主に変態温度+50℃前後ぐらいまで加熱した後、炉の中でゆっくりと冷却します。
そのため、対象物は炉から取り出すまでに長い時間がかかってしまいます。
1つの炉が、冷却のためだけに占領されてしまうのが欠点です。
焼なましのさまざまな目的を果たすためには、この「完全焼なまし」が必要ですが、軟化を目的にするだけであれば、「中間焼なまし」で十分対応できます。
これは冷却の際に、炉の外で空冷します。
そのほかにも、「拡散焼なまし」「球状焼なまし」「等温変態焼なまし」「応力除去焼なまし」などがあり、目的によって分けられます。
焼ならし
鋼の組織を均一にします。
部品の材料となる鋼材は、圧延などの熱間加工で作れていますが、できたそのままでは不均一な組織で、機械的性質は十分ではありません。
そのため、この焼ならしを行います。
焼準とも呼ばれ、英語ではノーマライジングと言います。これの目的は、鋼の内部応力の除去、鋼の材質改善などです。
焼ならしは、変態温度より高めの温度で加熱し、一定時間おいて内外の温度を一定にしたあと、空冷します。この時の加熱温度をきちんと設定することで、結晶粒が微細化され、強靭性などの機械的特性が得られます。またこれと同時に、残留応力も除去できます。
3Dプリンターによる造形
直接材料を製品の形に造形します。切削加工での製作など、従来の加工方法と比べて工数が少なく特に試作に向いています。
金属3Dプリンター造形方法一覧
レーザー焼結法 通称SLS(Selective laser sintering) |
粉末状の材料床(パウダーベッド)にレーザーを照射して一層ごとに焼結させる方法で、材料によっては従来の材質と同等に近い特性を実現することができるため、最終製品への利用が可能です。 表面の仕上がりにザラザラ感があり、滑らかさを表現する事は難しく、また装置が非常に大きいというのも特徴にあります。 |
直接金属レーザー焼結法 通称DMLS(Direct metal laser sintering) |
レーザー焼結方とほとんど同じ仕組みですが、レーザービームの原理が違います。 DMLSはほとんど全ての金属合金を造形することができるというメリットを持っています。 |
レーザー溶融法 通称SLM(Selective laser melting) |
レーザー溶融法は、SLS等と同じく粉末材料を使うのですが、材料を焼結ではなくレーザーで溶融して造形します。 精度が良く、材料を一度溶かすので表面の仕上がりは良好ですが、造形時間が長いという特徴があります。 |
電子ビーム溶解法 通称EBM(Electron Beam Melting) |
電子ビームを溶融源とし、パウダーベッドをデータ形状通りに溶融・凝固させる方法です。 EBMでは真空下で造形を行うのですが、真空装置が必要な分、装置が高価となるため普及が進んでいない原因のひとつになっています。 |
熱溶解積層法 通称FDM(Fused Deposition Modeling) |
FDM方式は樹脂3Dプリントで広く普及し、技術的進歩も進んでいたため、高性能で安価な装置が登場しています。 その他方式のように、防爆設備などの付帯設備を必要としないことも、低価格実現の後押しになっています。 この方式はノズルが動き、粉末ではなく棒状のフィラメント材を溶かして造形し、脱脂および焼結させることで、強固な製品が完成します。 |
レーザー直接積層法 通称LENS(Laser engineered net shaping) |
LENS方式は、粉末材料にレーザーを照射する仕組みとは違い、ノズルから粉末材料を射出する瞬間にレーザーを当てて焼結させ積層していく方法です。 この方式の一番の特徴は、SLS方式と比べて4倍速く造形できることです。 |
液体金属インクジェット3Dプリント (Liquid metal jet printing) |
インクジェットといえば樹脂3Dプリンターではおなじみですが、Xjet社(イスラエル)の開発により金属でも可能となりました。 金属だけでなく、セラミックスにも対応できるというのが驚きです。 Xjet社の装置では、1ミクロンの10分の1の大きさであるサブミクロンレベルで金属粒子を吹き付けることができるため、今まで表面のザラザラ感に課題があった金属3Dですが、比べ物にならないくらいに滑らかな表質と精度で造形することが可能になりました。 |
金属3Dプリンターで使用される材質とその特徴
マルエージング鋼
マルエージング鋼は、航空・宇宙分野の構造用向けに開発された材料で、金型にも使用されており、熱処理をすることで強度を高める(HRC50以上)ことが可能です。
高硬度で、高い靭性と機械的特性が備わっています。
アルミニウム
金属3Dプリンターで使用するアルミニウムはほぼ1種類で、AlSi10MgというSi(シリコン)含有のアルミニウム鋳造合金です。
金型レスで、アルミ鋳造品が小ロット生産できるというメリットがあります。
AlSi10Mg は強度、硬さ、靭性、機械的特性が良好で、アルミニウムなだけに軽量化目的の試作としても用いられます。
また、機械加工、放電加工、溶接を施すことができ、一般的なアルミダイキャストと同様にメッキ処理も可能ですので、広い用途に使用されます。
ステンレス
金属3Dプリンターで造形できるステンレスはSUS316LかSUS630です。
ステンレスですので、高強度、高硬度を必要とする部品に向いています。
用途としては治工具、構造部品、航空機部品などが多いです。
しかし、3Dプリンターで使用するステンレスの金属粉末は、切削加工等で使用される角材・丸材と比べて、材料費が10~20倍してくるのがネックとなりますので、高付加価値のある部品などに使用されることがほとんどです。
チタン
金属3Dプリンターで造形できるチタンは純チタンか64チタンです。
チタンは優れた機械特性と耐食性に、低比重と生体適合性を併せ持つ材質で魅力的ですが、3Dプリンターの中でも造形難易度が高い材料です。
特に造形途中に入るクラックや、熱歪みによる変形の可能性が高く、サポート材の付け方や造形方向をどうするか、というような知識・経験が必要になってきます。
インコネル
インコネル718という材料を3Dプリンターで造形できます。
切削するのも非常に難しい材質で、規格材料サイズも限られていたため、非常に高価な部品となっておりましたが、今では金属3Dプリンターで簡単に形状を作れるようになっているので、今後普及が期待されます。
金属加工のコストダウン方法
金属加工を検討される際に、コストは抑えたいポイントになります。
ここでは、金属切削加工においてコスト要因として挙げられる材料代と加工内容の削減ポイントをお伝えします。
材料代
材料選定時にコストを抑える為のポイントは、材料費と加工性です。
まず、材料費を抑えるためには安価な材料を使用する必要があります。
例えば、切削加工で一般的によく使用されるSS400やS45Cなどの材質は入手性も高く、切削材の中では比較的安価です。
次に重視していただきたいのが加工性です。
刃物で切削をする際に削りやすく、加工時間が長くかからない材質は加工費を抑えることができます。
例えば銅や真鍮といった材質は快削なので硬度が高く、ステンレスなどの切削に時間のかかる材質よりもコストを抑えやすくなります。
使用目的が治具のように材料選定に細かい指定がない場合は、上記二点を参考にしてください。
硬度やサビに強い材質が必要など材料選定の基準がある場合は、その内容をお伺いできればご指定の条件に対応できる材質や、表面処理や焼入れといった方法も考慮し、コストダウンできるよう検討致しますのでお気軽にご相談ください。
加工内容
切削加工時にコストを抑えられるポイントは以下のものがあります。
公差の緩和
100分台など細かく公差の指定が入っている加工の場合は、寸法を公差内に入れるため、より精密な加工を行うことになり加工費のコストが高くなります。
お見積り時に加工品の使用方法や、使用する際に必要な精度をお伺いし、必要超過分の公差の緩和をすることができれば加工費を下げられることがあります。
また、嵌め合いの公差を設定されている場合も、実際に嵌る相手部品をご支給いただければ、嵌合確認をしながらの加工となり嵌め合い公差を緩和できる場合がありますので、加工費用は抑えやすくなります。
工程数の削減
加工に必要な工程数を削減することができれば、加工時間を減らすことができる為、コストを抑えやすくなります。
例えば加工をする際に治具の製作も必要な加工品の場合、設計の変更を行うことで治具製作が必要なくなれば加工費が下がります。
図面をお預かりした際に、コストダウンの為に削減可能な箇所があればご提案させて頂きます。
寸法の設定
材料の選定や工程数の削減とも関わる内容になりますが、外寸の設定もコストダウンに繋がることがあります。
例えばΦ52で設定されていた外径をΦ50やΦ55など、もともと材料の規格にある大きさにすれば外径を削る必要がなくなり、費用を抑えやすくなります。(※1)
板材からの加工の場合は、厚みを設定していただく際に材料の規格をご考慮いただければ6面フライス加工をする必要がなくなり、加工時間を短縮できる場合があります。
外寸の規格については材料によって大きさが異なりますので、ご検討される場合は是非お見積り時にご相談ください。
※1…材質によっては素材のままだと外径に黒皮がついている状態の物もあり、外径を削る必要がある為コストダウンに繋がらない場合もあります。
時間のかかりやすい加工内容の変更
公差の指定などがなく、簡単に見える加工内容でも実際には加工時間のかかるものがあります。
《例1》深い穴を開ける必要がある場合
穴の大きさがブレないようドリルを入れての加工になりますので、加工時間がかかりやすいです。
こういった場合、差し支えがなければ穴を貫通穴に変更していただくことで加工コストを抑えられる場合があります。
《例2》一体物として製作する場合に加工時間のかかる部品
部品にピンのような細長い形状の突起がある場合、削り出しで突起部分を加工すると時間がかかります。
こういった形状の場合は基となる部品に穴を開け、ピンを差し込みネジなどで固定することで加工コストの削減に繋がることがあります。
3Dデータのご支給
図面のみでなく3Dデータを御支給いただければ、マシニングにプログラミングデータを入力する時間が削減できる為、加工費を抑えることができます。
平面の図面や2Dのdxfデータのみだと加工方法の確認が難しい箇所も、3Dデータがあれば形状を確認することができる為、加工ミスを防ぎ、複雑な形状でもより正確に加工を進めることが可能というメリットもあります。
メタルスピードではSTEP、IGS、パラソリッドなどの拡張子に対応が可能です。
金属加工について、コストを抑える方法をご紹介させて頂きましたが、実際にコストを意識しながら材料の選定を行ったり、設計をされるのは難しいことだと思います。
メタルスピードでは担当の営業がお客様のご要望をヒアリングし、柔軟に対応させていただいております。
加工費用を抑えたい場合は具体的なご希望単価を教えていただければ、ご要望に沿えるよう尽力致します。
また、納期も単価に関わる大きな要素となっております。
納期によってはコストダウンにご協力できる場合がございますので、加工内容と合わせてお見積りの際にご相談ください。
お見積り・お問い合わせ
無料お見積り2時間以内に返答対応
メールでのご連絡は
info@metal-speed.com まで
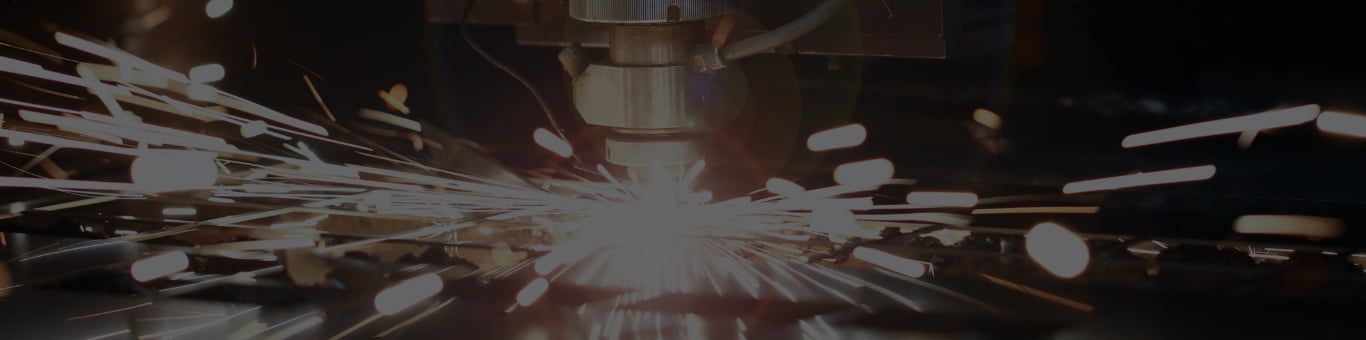